In the 1950s and 60s, the earliest versions of CAD software began to change the way that companies did product development. Where before calculations and drawings had to be done almost entirely by hand, engineers could now do faster, more robust design and development work with the aid of specialized computer programs.
Wow, what a revolution! Most of the exciting advances in engineering design that we see all around us were facilitated on some level by the use of computer software.
It has been many decades since the software revolution began. These days, it seems there is a specialized piece of software for everything an engineering company might need. Need to design parts in 3D? There are about 50 CAD programs to choose from, such as Siemens NX, Creo, Catia, Solidworks, etc. Need to perform simulation? You’ve got several great options, such as Simcenter or Ansys. There is software for CAE, CAM, FEA. If all else fails, C++, Python, Java can help with custom software solutions. And of course, Excel is a tried and true option for any number of engineering tasks – kind of like duct tape for the design process.
The boom of resources and innovation from the software industry is inspiring and exciting.
But like most things in life, even this has a downside: too much software.
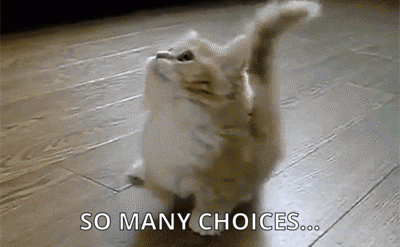
Unfortunately, the abundance of software resources on the market today can lead to a kind of software creep. Companies end up with so many disparate solutions in use on a single project that coordinating them all becomes a job in and of itself.
Rather than facilitating better design, juggling too many different pieces of software can leave engineers and project teams overwhelmed. The multi-step, often tedious or confusing processes engineers and teams have to use to coordinate their work across multiple disparate software programs can easily become a distraction that sucks unnecessary time and energy away from the real work of the project.
Tolerance stack analysis is no exception.
CAD software can do great things to help with the R&D process. It does a great job drawing, designing, and modeling. Some software, such as Creo, can put GD&T labels within the drawing and can even do basic tolerance analysis.
One of the biggest problems engineers face today is not actually building tolerance stacks. These can even be done in Excel. The problem arises when there are volumes of stacks but engineers are not sure which ones to update, should a part design change. The fragmented use of various software to manage the product life cycle and facilitate collaboration when a part is changed leads to confusion, mistakes, and gaps in efficiency.
During R&D, design changes happen frequently as design engineers work with senior engineers to do necessary fine-tuning. Many times this forces engineers to go back to the drawing board. This is a time-consuming process. Simulation software tries to help. But the complexity of most simulation software is only justified for complex problems.
Then, when things are finalized, the product goes to manufacturing. Another set of software is used to help with FAI, DFMEA, Monte-Carlo and other manufacturing-related processes.
This is where Tolerance360 can help. Tolerance360 is a collaborative software that glues together team activities related to tolerance analysis from design to manufacturing. With its workflow feature, everyone stays updated on what is relevant. With the auto-update feature, stacks can always be updated with part design change or flag a bad update that will cause issues. Design changes do not need to originate from the CAD design drawing board. Changes can be software-defined or virtual, shaving the time needed in development. T360 simply connects the dots between design, engineering, and manufacturing.