In 2007’s Next¸ Cris Johnson (played by Nicholas Cage) has a superpower: he can see into his own future, but only by 2 minutes. This power proves to have a variety of uses, such as when he uses his 2 minutes of foresight to try out different ways of approaching a girl in a diner. He tries one approach after another, letting each play out 2 minutes into the future so that he can judge the girl’s response. He is rejected time and again until at last he finds the approach that works – armed with foresight, this is the method he uses in reality, and of course he gets the girl.
In essence, Cris Johnson’s unique ability allows him to test out different scenarios, assess outcomes, and use what he learns to make data-driven decisions on how to act. As engineers, we may not have Cris Johnson’s superpower, but we can come pretty close thanks to Monte Carlo simulation.
What is Monte Carlo simulation? Monte Carlo Simulation is a mathematical modeling technique that allows you to see all possible outcomes and assess risk to make data-driven decisions. It basically uses random numbers to simulate random effects. This is done many times in order to measure variation as if you were producing many samples of a real event. This allows many complex effects to be simulated quickly vs actual experimentation since a computer can perform the simulation.
There are several types of Monte Carlo probability distributions including Normal, Lognormal, Uniform, Poisson and Triangle. Each distribution type is used based on the subject of the modeling. Depending on the selected distribution type the simulation on the model is run many times using different variables and the results of these simulations are generally represented graphically The more iterations are run, the more accurate results will be.
The advantage of Monte Carlo simulation is that it considers a wide range of possibilities to help reduce risk and uncertainty over other tolerance analysis methods.
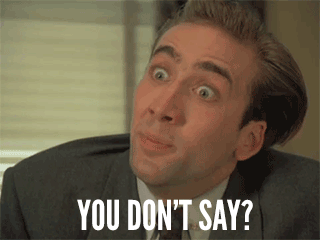
With engineering tolerance analysis, Monte Carlo simulation is used when you want to further analyze tolerance stacks that have many dimensions or non-linear parts. It can be used to determine how many assemblies may be outside the desired tolerance range. With your results you can then explore changing the tolerance requirements as long as manufacturing can support the changes.
T360 integrates advanced analysis, including Monte Carlo simulation, directly into the input and analysis screen. Once a stack is created, you can use other features to analyze stacks including Sensitivity Analysis, What-If, and FAI inspection analysis.
Users can provide (1) Target Sigma (3s as default) and (2) Standard Deviation.
Run. The application performs a Monte Carlo simulation technique to analyze the current stack statistically based on the setup values. At the end of the run, a mean value which is equivalent to the Nominal value of Vector Sum and a standard deviation which is equivalent to the RSS value/3.
In summary, Monte Carlo simulation is a way to use engineering knowledge and more subjective evaluation of inputs to create a quantitative output. In reality, all of the models that you create will have flaws. The Monte Carlo method provides an entire, detailed view of results which allows you to understand how your design performs without needing to make excessive amounts of manual calculations in a typical spreadsheet or excessive real life sample testing.
And that’s it! Armed with Monte Carlo simulation techniques, you too can wield the power of foresight to make data-driven decisions. Here’s a wink from Nic Cage to remind you how awesome that is:
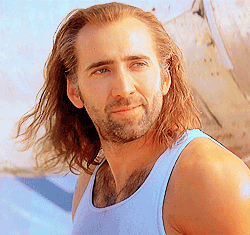
(Yes, we know this version of Nic Cage is from Con Air – but let’s face it, that was a much better movie. Now go forth and simulate!)