One of the keys to an effective mechanical design process is the ability to quickly identify design faults or make changes to a design to achieve proper part tolerances and fit.
In most design processes, a drawing is created with CAD software and the GD&T associated with those parts is used to perform tolerance analysis. If those parts do not meet the proper tolerance analysis criteria or a design change needs to be made, the usual process is to return to the design team and make changes within CAD drawings.
The problem with this process is that it is time-consuming, inefficient, and not very cost-effective. Complex projects may require numerous iterations and revisions.
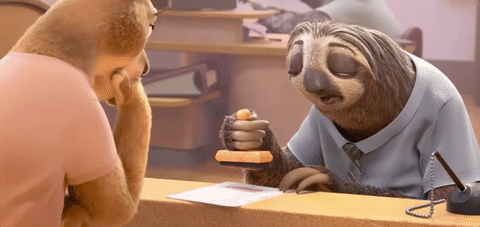
The more complex the project, the more likely that slow-downs will occur.
Virtual Parts: A new approach to design and tolerance analysis
With T360’s Virtual Part feature, engineers can create virtual parts directly inside of the T360 system that can be used to improve the design or correct any faults. Virtual parts even allow an engineer to include non-dimensional data like testing results or FEA analysis.
Virtual parts can also allow for complex behavior, movement and angles. Further, virtual parts can be used within each other which allows engineers to experiment with a multitude of design options and hypothetical solutions. The biggest benefit of virtual parts is that they can be updated automatically when other parts in the design are changed in relation to the virtual part.
By removing the need to return to the CAD design team for every change or correction, engineers save vast amounts of time in finalizing the design process which reduces the total cost of a project.
With these advances, the T360 software represents a paradigm shift in the way the traditional design process happens, from time and resource-consuming revisions to a much more efficient and cost-saving operation.
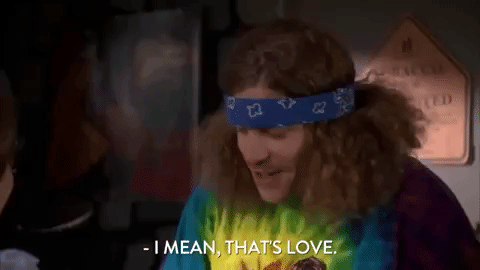