When it comes to manufacturing, GD&T is still king. GD&T is the language that translates the 3D world to paper design drawings. This low cost, simplistic, tried & true method is a platform where all parties – from designers, to engineers, to manufacturers – can speak to and understand each other. This is why Tolerance 360 uses GD&T instead of 3D data.
While 3D modeling has its own advantages, it has created an additional layer of complexity in the design process, especially when design changes need to be made. Design intent can also be more difficult to convey to manufacturers. 2D and 3D are both still needed to show product manufacturing information.
When considering tolerance analysis, 2D and 3D analysis become much more difficult and susceptible to errors if done by hand. There are several 2D/3D tolerance analysis software programs, but they require high levels of training and take a long time to produce results. Making updates to the design only increases the time it takes to update tolerance analysis as much of this 3D software does not have the ability to automatically integrate new design data changes.

Oftentimes, 3D tolerance analysis is not needed to accurately analyze an assembly at all. In these cases, 1D tolerance analysis is a quicker, easier tool.
1D analysis cuts down on the design cycle time because it can be easily updated and analyzed, allowing engineers to move quickly through the development cycle. Five important reasons to use 1D vs 2D or 3D tolerance analysis include:
- 1D analysis is uncomplicated and can handle a majority of tolerance needs for a majority of part assemblies (>80%).
- 1D tolerance analysis can be done quickly and easily to validate part assembly and design intent which allows for easier updates.
- Tools and software that are used to calculate using 3D models can be cumbersome, difficult, and time-consuming and require additional training vs 1D tools.
- As the number of components and complexity increases tolerance contributions, 1D stackup analysis allows engineers to quickly and confidently know, with reasonable certainty, that design intent will be met. This will save costs on manufacturing and potential revisions during testing or production phases.
- Engineers can use a variety of 1D analysis types from worst-case, RSS, or statistical analysis to help prevent quality issues, rework, and manufacturing variations.
These are just a handful of the reasons why it’s worth considering 1D tolerance analysis. It’s a bit like heading out to buy a new television – you don’t need to take an airplane to the electronics store, and you also don’t want to lug the television back on your bicycle. The quickest, easiest, most efficient way of getting there and back is probably your car. 1D tolerance analysis is often the quickest, easiest, most efficient way of accurately analyzing an assembly or stack and communicating the information to various players.
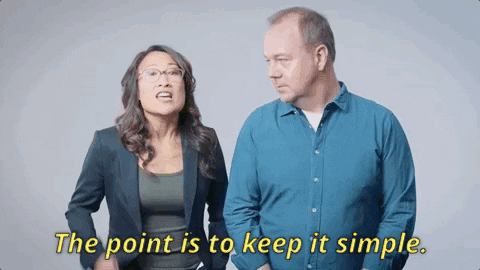